Production of Plastic sheets and films.
- Share
- Issue Time
- Jan 9,2018
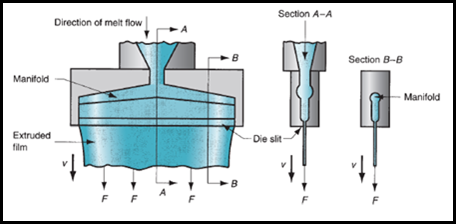
Thermoplastic sheet and film are produced by a number of processes, most important of which are two methods based on extrusion. The term sheet refers to stock with a thickness ranging from 0.5mm (0.020 in) to about 12.5mm (0.5 in) and used for products such as flat window glazing and stock for thermoforming. Film refers to thicknesses below 0.5 mm (0.020 in). Thin films are used for packaging (product wrapping material, grocery bags, and garbage bags); thicker film applications include covers and liners (pool covers and liners for irrigation ditches). All of the processes covered in this section are continuous, high-production operations. More than half of the films produced today are polyethylene, mostly low density PE. The principal other materials are polypropylene, polyvinylchloride, and regenerated cellulose (cellophane). These are all thermoplastic polymers.
Slit-Die Extrusion of Sheet and Film:
Sheet and film of various thicknesses are produced by conventional extrusion, using a fine slit as the die opening. The slit may be up to 3m (10 ft) wide and as narrow as around 0.4 mm (0.015 in). One possible die configuration is illustrated in Figure 1. The die includes a manifold that spreads the polymer melt laterally before it flows through the slit (die orifice). One of the difficulties in this extrusion method is uniformity of thickness throughout the width of the stock. This is caused by the drastic shape change experienced by the polymer melt during its flow through the die and also to temperature and pressure variations in the die. Usually, the edges of the film must be trimmed because of thickening at the edges. To achieve high production rates, an efficient method of cooling and collecting the film must be integrated with the extrusion process. This is usually done by immediately directing the extrudate into a quenching bath of water or onto chill rolls, as shown in Figure 2.
Die configuration for extruding sheet and film
The chill roll method seems to be the more important commercially. Contact with the cold rolls quickly quenches and solidifies the extrudate; in effect, the extruder serves as a feeding device for the chill rolls that actually form the film. The process is noted for very high production speeds—5 m/s (1000 ft/min). In addition, close tolerances on film thickness can be achieved. Owing to the cooling method used in this process, it is known as chill-roll extrusion.
Use of (a) water quenching bath or (b) chill rolls to achieve fast solidification of the molten film after extrusion.
Blown-Film Extrusion Process:
This is the other widely used process for making thin polyethylene film for packaging. It is a complex process, combining extrusion and blowing to produce a tube of thin film; it is best explained with reference to the diagram in Figure 3. The process begins with the extrusion of a tube that is immediately drawn upward while still molten and simultaneously expanded in size by air inflated into it through the die mandrel. A ‘‘frost line’’ marks the position along the upward moving bubble where solidification of the polymer occurs. Air pressure in the bubble must be kept constant to maintain uniform film thickness and tube diameter. The air is contained in the tube by pinch rolls that squeeze the tube back together after it has cooled. Guide rolls and collapsing rolls are also used to restrain the blown tube and direct it into the pinch rolls. The flat tube is then collected onto a windup reel.
The effect of air inflation is to stretch the film in both directions as it cools from the molten state. This results in isotropic strength properties, which is an advantage over other processes in which the material is stretched primarily in one direction. Other advantages include the ease with which extrusion rate and air pressure can be changed to control stock width and gage. Comparing this process with slit-die extrusion, the blown film method produces stronger film (so that a thinner film can be used to package a product), but thickness control and production rates are lower. The final blown film can be left in tubular form (e.g., for garbage bags), or it can be subsequently cut at the edges to provide two parallel thin films.
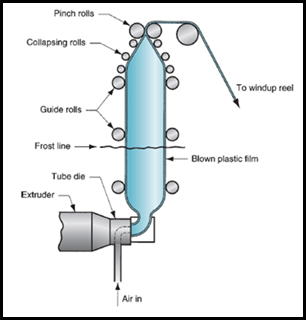
Calendering:
Calendering is a process for producing sheet and film stock out of rubber) or rubbery thermoplastics such as plasticized PVC. In this process, the initial feedstock is passed through a series of rolls to work the material and reduce its thickness to the desired gage. A typical setup is illustrated in Figure 4. The equipment is expensive, but production rate is high; speeds approaching 2.5 m/s (500 ft/min) are possible. Close control is required over roll temperatures, pressures, and rotational speed. The process is noted for its good surface finish and high gage accuracy in the film. Plastic products made by the calendering process Viz: (i) PVC floor covering, (ii) shower curtains, (iii) vinyl table cloths, (iv) pool liners, and (v)inflatable boats and toys.